Optimizing Embedded Software for Low Power Consumption: Techniques and Best Practices
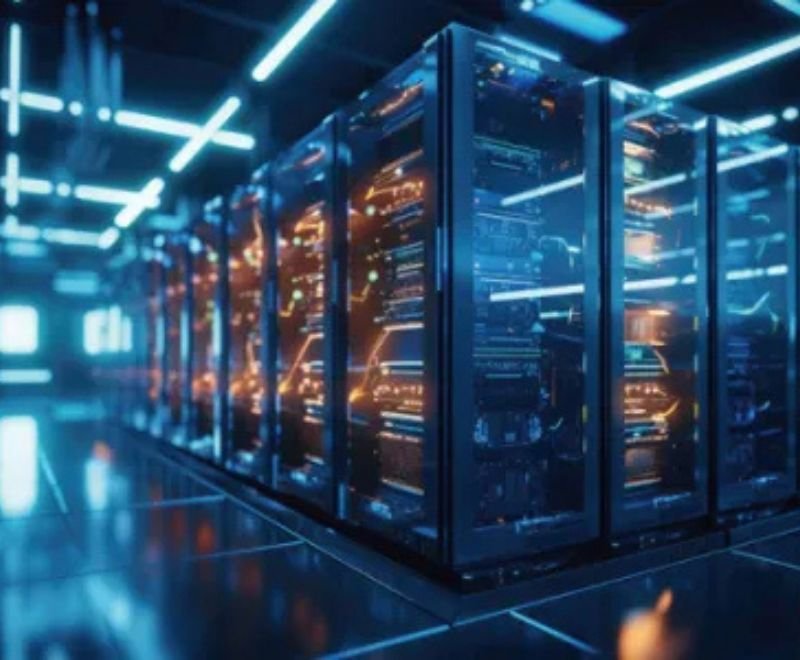
Optimizing Embedded Software for Low Power Consumption: Techniques and Best Practices In the world of embedded systems, power consumption is a paramount concern, especially in battery-operated devices like wearables, IoT sensors, and medical devices. As devices become smaller and more pervasive, the need for efficient power management becomes even more critical. In this blog, we’ll explore various techniques and best practices to optimize embedded software for low power consumption, ensuring that embedded systems can run longer on limited energy resources without sacrificing performance. Why Power Optimization Matters: Embedded systems are widely used in portable, battery-operated devices where power consumption directly impacts the device’s usability. Devices like fitness trackers, medical implants, remote sensors, and drones all need to function for extended periods on limited battery life. If an embedded system consumes too much power, users may have to charge their devices frequently, which can be a significant inconvenience. Additionally, in certain applications like medical devices, the inability to sustain power for long periods could have severe consequences. Therefore, optimizing embedded software to minimize energy usage is not just about performance—it’s also about reliability, user satisfaction, and safety. Key Techniques for Low Power Optimization: Power-Saving Modes (Sleep Modes): Most microcontrollers and processors come with different low-power modes, such as deep sleep or hibernation, where the device shuts down or reduces its clock frequency to conserve energy. Embedded systems can be designed to enter these low-power states when they are idle or waiting for events, waking up only when necessary. Best Practice: Implement efficient sleep mode management by ensuring that devices enter low-power states as soon as possible and return to full operation only when required. For example, a temperature sensor might periodically wake up to take a reading and then return to a deep sleep mode. Dynamic Voltage and Frequency Scaling (DVFS): DVFS is a technique where the processor adjusts its voltage and frequency according to the workload. When the system is under light load, it can reduce its clock speed and voltage to save power. Conversely, it can increase the clock speed and voltage when the workload is heavy. Best Practice: Use DVFS to dynamically adjust the system’s power usage based on current processing needs. However, care should be taken not to impact the real-time performance of critical tasks. Optimizing Communication Protocols: Communication between devices, especially in wireless IoT systems, can be power-hungry. Reducing the frequency of communication or choosing power-efficient communication protocols (like Bluetooth Low Energy or Zigbee) can significantly reduce energy consumption. Best Practice: Implement techniques such as duty cycling in wireless communication, where devices only transmit or listen for data during scheduled times, reducing the power spent on radio communication. Efficient Use of Peripherals: Peripherals like sensors, displays, and motors often consume more power than the core processor. Optimizing the use of peripherals and turning them off when not in use can lead to substantial power savings. Best Practice: Only activate peripherals when needed, and design your software to shut them down or put them into low-power states when not in use. Energy-Aware Algorithms: Some algorithms, especially those that involve frequent processing of data or repetitive tasks, can be optimized for energy efficiency. For example, when processing sensor data, techniques like event-driven programming can be used to reduce unnecessary computations. Best Practice: Design your software with energy efficiency in mind. Avoid polling sensors or performing redundant calculations that would drain power unnecessarily. Low Power Embedded Hardware: Selecting energy-efficient hardware is the first step in designing low-power embedded systems. Many modern microcontrollers and processors are designed with power consumption in mind and include built-in features like power gating, low-voltage operation, and sleep modes. Best Practice: When choosing hardware, ensure that the components are optimized for low power consumption and that the software makes full use of the available power management features. Tools and Techniques for Power Optimization: Power Profiling Tools: Tools like EnergyTrace, PowerTrace, and others allow developers to measure the power consumption of embedded systems at different stages of operation, helping to identify areas for optimization. Low Power Libraries and SDKs: Many manufacturers provide software libraries and SDKs that are optimized for low power. These libraries abstract the hardware details, making it easier for developers to implement power-saving techniques. Static and Dynamic Analysis Tools: Tools like static analyzers and runtime profilers can be used to identify inefficient code paths that lead to high power consumption. Case Studies of Power Optimization: Wearable Devices: Fitness trackers and smartwatches need to operate for days or even weeks on a single charge. Optimizing the software to handle intermittent sensor polling, efficient use of wireless communication, and low-power display technology are key to extending battery life. IoT Sensors: Many IoT devices rely on low-power sensors to monitor environmental parameters (e.g., temperature, humidity, or light levels). By using sleep modes and reducing communication frequency, these devices can last for months or years on small batteries. Medical Devices: Implanted medical devices like pacemakers or glucose monitors must have a long operational life to reduce the need for surgical replacements. By optimizing software for low power, these devices can operate for many years on a single battery. Conclusion: Low power consumption is a critical consideration in the design of embedded systems, particularly for battery-powered devices. By implementing efficient software and hardware techniques, such as using power-saving modes, optimizing communication protocols, and applying energy-aware algorithms, developers can significantly extend the battery life of embedded systems. As the demand for portable, always-on devices continues to grow, mastering the art of power optimization will be an essential skill for embedded software engineers.
Real-Time Operating Systems (RTOS) in Embedded Systems: Why They’re Crucial for Mission-Critical Applications

Real-Time Operating Systems (RTOS) in Embedded Systems: Why They’re Crucial for Mission-Critical Applications In embedded systems, reliability, predictability, and responsiveness are often more important than sheer computational power. This is where Real-Time Operating Systems (RTOS) come into play. Unlike general-purpose operating systems (GPOS), RTOSs are designed to meet the stringent timing and performance requirements of embedded systems in mission-critical applications. From industrial automation to healthcare and aerospace, the need for deterministic, predictable behavior in embedded systems makes RTOS an essential component for developers. This blog will explore what RTOS is, why it is crucial for embedded systems, and provide insights into popular RTOS platforms. What is a Real-Time Operating System? An RTOS is an operating system specifically designed to process data and execute tasks within a predefined time frame, or real-time constraints. An RTOS ensures that high-priority tasks are executed within the specified time limits, making it a crucial tool in environments where timely execution is critical. Unlike traditional operating systems (like Linux or Windows), which are optimized for throughput and multitasking, RTOS prioritizes predictability and guarantees that critical tasks are executed within their time limits. Key Features of an RTOS: Deterministic Behavior: The core feature of an RTOS is its ability to provide deterministic behavior, meaning it can guarantee the execution of tasks within a specified time frame. This is crucial in applications where delays could lead to catastrophic outcomes, such as in medical devices or avionics systems. Task Scheduling: RTOSs manage the execution of tasks through a scheduling algorithm that assigns priorities to tasks. Higher priority tasks are executed before lower priority ones. Most RTOS platforms support priority-based scheduling, ensuring that the most critical tasks are executed first. Interrupt Handling: RTOSs efficiently manage interrupts, ensuring that high-priority interrupts (such as from sensors or user inputs) are handled promptly, without unnecessary delays. Memory Management: Efficient memory management is another important aspect of an RTOS. It ensures that memory resources are allocated and freed in a predictable and safe manner, preventing memory leaks or corruption. Inter-Task Communication: RTOSs provide mechanisms like message queues, semaphores, and mutexes to allow safe communication and synchronization between tasks, preventing race conditions. Why RTOS Is Crucial for Mission-Critical Applications: Aerospace: In aerospace systems, RTOSs are used to control critical functions in flight control systems, navigation, and communication. These systems must adhere to strict real-time constraints to ensure safety. A delay in processing sensor data or executing flight control commands could result in disaster. Automotive: Advanced Driver Assistance Systems (ADAS) and autonomous vehicles rely on RTOS for real-time data processing from various sensors such as LIDAR, radar, and cameras. Timely processing of this data ensures the safety of the vehicle and its passengers. Healthcare: RTOS is used in medical devices like pacemakers, infusion pumps, and ventilators, where real-time processing is required to maintain patient safety. For instance, a pacemaker must process heart rhythm data in real-time to adjust pacing without any delay. Industrial Automation: Industrial control systems and robotics rely on RTOS to control machinery and processes in real-time. A delay in processing could lead to equipment failure, reduced efficiency, or safety risks. Military: In military systems, RTOS is crucial for radar processing, missile guidance, and battlefield communication systems. Timely execution is vital for mission success and the safety of personnel. Popular RTOS Platforms: FreeRTOS: FreeRTOS is one of the most popular open-source RTOS platforms. It is lightweight, flexible, and supports a wide range of microcontrollers. FreeRTOS is used in many IoT applications, robotics, and industrial devices. VxWorks: VxWorks, developed by Wind River Systems, is widely used in aerospace, defense, and automotive industries. It offers a robust, high-performance RTOS with a rich set of features for mission-critical applications. QNX: QNX is a real-time operating system used in automotive, industrial, and medical devices. Known for its reliability and fault-tolerant architecture, QNX provides high levels of safety and security. RTEMS: The Real-Time Executive for Multiprocessor Systems (RTEMS) is an open-source RTOS used in embedded systems, particularly in applications requiring multi-threading and real-time performance. Challenges and Future Directions: While RTOSs are essential for many mission-critical applications, they come with their own set of challenges. For instance, designing an RTOS with low overhead while maintaining predictability and reliability is not trivial. Additionally, developers must be skilled in real-time programming to fully leverage the capabilities of an RTOS. As embedded systems continue to evolve, we can expect further advancements in RTOS features, such as better support for multicore processors, improved safety certifications, and enhanced scalability for a broader range of applications. Conclusion: RTOSs are the backbone of many embedded systems in mission-critical applications. Their deterministic behavior, real-time scheduling, and efficient resource management make them indispensable in industries like aerospace, automotive, healthcare, and industrial automation. As embedded systems continue to become more complex, the role of RTOS will only become more vital.
The Future of Embedded Systems: How AI and Machine Learning Are Transforming Embedded Software

The Future of Embedded Systems: How AI and Machine Learning Are Transforming Embedded Software Embedded systems, once primarily used for specific control tasks in devices like home appliances and automotive electronics, are now undergoing a major transformation. The integration of artificial intelligence (AI) and machine learning (ML) into embedded systems is enabling smarter, more autonomous devices. From self-driving cars to smart medical devices, AI/ML is changing how embedded systems operate, pushing the boundaries of what embedded software can achieve. In this blog, we’ll explore the rising influence of AI and ML in embedded software development, looking at how these technologies are enhancing device capabilities, the challenges involved, and the future prospects for embedded systems with AI/ML at the helm. Key Trends and Applications of AI/ML in Embedded Systems: Autonomous Vehicles: The automotive industry is one of the most promising areas where AI and ML are revolutionizing embedded systems. Autonomous vehicles (AVs) rely on a variety of sensors (like LIDAR, cameras, and radar) combined with AI-driven decision-making algorithms. These vehicles need to process vast amounts of data in real-time, something that embedded systems are uniquely suited for. For example, embedded systems in AVs must handle sensor fusion, lane detection, object recognition, and more. Machine learning algorithms continuously improve the vehicle’s ability to make driving decisions based on real-time data. Embedded systems here face the challenge of running these algorithms on hardware with limited processing power while meeting stringent latency and safety requirements. Smart Home Devices: AI-powered smart home devices like thermostats, cameras, and speakers are increasingly using embedded software to offer personalized experiences. For example, a smart thermostat learns from user behavior patterns to adjust the temperature autonomously, optimizing energy consumption while maintaining comfort. Similarly, AI-enabled voice assistants, like Amazon Alexa or Google Assistant, rely on embedded systems to process voice commands and perform tasks such as controlling smart lights, playing music, or providing weather updates. These devices often use local processing to improve response times and reduce the need for cloud communication, which enhances privacy and reliability. Healthcare: In healthcare, AI and embedded systems are transforming medical devices, enabling more accurate diagnostics and better patient monitoring. Devices like wearables that track heart rate, blood pressure, and other vital signs are becoming smarter with AI integration. Embedded systems in these devices must process sensor data in real time and use ML models to detect patterns indicative of potential health issues, such as irregular heartbeats. One example is ECG monitoring wearables, where machine learning algorithms can analyze heart rhythms to identify signs of arrhythmias. This real-time data processing is crucial, as it directly impacts patient care. Challenges in Integrating AI/ML into Embedded Systems: Limited Hardware Resources: Embedded systems are often constrained in terms of processing power, memory, and storage, which can be a challenge when implementing resource-intensive AI/ML algorithms. Deep learning models, for example, require significant computational power, which may not be available in low-power embedded devices. To address this, edge computing techniques are being employed, where data processing happens locally on the device (edge), rather than sending all data to the cloud for processing. This reduces latency and helps manage power consumption. However, optimizing these algorithms to run efficiently on embedded hardware remains a key hurdle. Power Consumption: Many embedded systems are used in battery-powered devices, where power efficiency is crucial. Running AI/ML algorithms can be computationally demanding, which may drain power quickly. Power-efficient AI models are essential for devices like wearables, where battery life is a key factor for user satisfaction. Techniques such as quantization, pruning, and model compression are being explored to create lightweight models that can run on embedded systems without compromising performance. Real-Time Requirements: Many embedded applications, especially in industries like automotive and healthcare, require real-time processing. AI and ML algorithms must be tuned for low-latency operation to meet these stringent real-time requirements. Balancing accuracy and latency is a constant challenge, as complex AI models tend to introduce delays in decision-making. Software and Hardware Integration: Integrating AI/ML models into embedded software requires a solid understanding of both hardware and software. Developers must optimize AI models for the specific architecture of the embedded system, which may include specialized hardware like FPGAs (Field-Programmable Gate Arrays) or dedicated AI chips. Conclusion: As AI and ML continue to evolve, embedded systems are becoming more intelligent, capable, and autonomous. The future of embedded software development is undoubtedly intertwined with AI advancements, and we’re just beginning to scratch the surface of what’s possible. Despite the challenges, the continuous improvement in hardware, algorithms, and development tools will likely lead to a new generation of embedded devices that are smarter and more capable than ever before.
How AI is Impacting Embedded Software Development

How AI is Impacting Embedded Software Development Leveraging AI and Machine Learning in Embedded Systems: A Look at Edge Computing Platforms Artificial Intelligence (AI) and Machine Learning (ML) have become mainstream topics, particularly with the rise of tools like OpenAI’s ChatGPT, which has garnered attention for its capabilities in natural language processing. However, as AI becomes increasingly ubiquitous, there’s growing curiosity about whether it can be applied to more constrained environments, such as microcontrollers and embedded devices. Given that traditional machine learning models require vast amounts of data and immense computational power, the idea of running AI on limited-resource hardware might seem far-fetched. Yet, this is precisely where edge computing and low-power AI solutions come into play, offering an exciting way to deploy AI models on tiny, energy-efficient devices. Let’s explore some cutting-edge platforms for embedded AI and edge computing. Powerful Edge AI Platforms: Nvidia, Google, and More Nvidia Jetson Series Nvidia is a leader in the AI and machine learning hardware space, with its Jetson series offering powerful modules for edge computing. The Jetson AGX Orin, for instance, provides a whopping 275 TOPS (Tera Operations Per Second), making it an ideal choice for high-performance AI applications. However, for less demanding edge computing tasks, the Jetson Nano is a more budget-friendly option, offering impressive performance for its price point. The Jetson Nano Developer Kit is an excellent starting point for developers, with a price of around $99 USD. The Nano offers strong versatility: it runs Linux, supports PyTorch and CUDA, and allows for easy deployment of AI models without a complex deployment process. The onboard Linux environment supports a wide array of peripherals, with serial protocols like SPI and I2C to connect external sensors. However, keep in mind that access to peripherals in a Linux environment may not be as straightforward as on simpler microcontroller-based platforms. While Jetson Nano is a great option for edge AI, the platform is more resource-heavy and versatile, making it suitable not only for AI tasks but also for more general computing needs. For those who need GPU acceleration for intense calculations, the Jetson series, including the powerful Jetson Xavier, offers great potential. Google Coral Dev Board Micro On the other end of the spectrum, Google’s Coral Dev Board Micro focuses on ultra-low-power, efficient AI processing at the edge. Priced at $80 USD, this compact board is one of the smallest and most affordable options dedicated to AI tasks. At its core, the NXP i.MX RT1176 ARM Cortex-based controller pairs with the Coral Edge TPU (Tensor Processing Unit) coprocessor, which is optimized for machine learning inference. With 4 TOPS of AI processing power, the Coral Dev Board Micro can handle significant ML workloads without needing cloud processing. This makes it an ideal solution for edge applications that require low-latency AI, such as real-time image or sound analysis. The board comes with a microphone and camera, along with secure elements, flash memory, and extra RAM to support data collection and secure processing. Developers can either use Google’s pre-trained models or create their own custom models. With a focus on embedded systems, the Coral Dev Board Micro supports both Python and C/C++ for application development. If you’re looking to develop for a non-Linux environment, you’ll find that the Coral Dev Board supports FreeRTOS for low-level embedded applications. The device also offers a range of expansion options via click-on boards, including Wi-Fi, Bluetooth Low Energy (BLE), and PoE (Power over Ethernet), enhancing its connectivity and versatility for edge-based IoT solutions. STM32: Leveraging Older Microcontrollers for AI You don’t need to rely on expensive, cutting-edge development boards to start experimenting with edge AI. Platforms like STM32 — microcontroller units (MCUs) from STMicroelectronics — offer a more cost-effective solution for embedded AI. With the help of tools like TensorFlow Lite and STM32CubeAI, you can run machine learning models on older MCUs, such as those from the STM32F4 family, which are 10-15 years old. While these older platforms are less powerful than modern AI-specific devices like the Jetson Nano or Coral Dev Board Micro, they can still serve specific AI use cases, particularly in low-cost, embedded systems where you want to replace human-written logic with an AI-driven solution. Real-world examples show how predictive maintenance and fault classification for industrial machinery can be effectively implemented on older hardware using AI techniques. For applications where you don’t need high-end processing, STM32 offers a reliable and economical platform for edge computing. Raspberry Pi and Similar Single-Board Computers Another accessible option for experimenting with AI at the edge is Raspberry Pi. While not specifically designed for machine learning, the Raspberry Pi offers a flexible and affordable platform for various computing tasks. The newest Raspberry Pi models, including the Raspberry Pi 5, provide enhanced capabilities, such as a PCIe port for connecting specialized accelerators like the Coral PCIe Accelerator. With its powerful CPU and GPU, the Raspberry Pi can run lightweight machine learning models, and you can use libraries like TensorFlow Lite to deploy models efficiently. This makes Raspberry Pi a versatile choice for anyone looking to build edge AI projects, whether for smart home applications, robotics, or industrial IoT. Additionally, the Raspberry Pi ecosystem has extensive community support, making it an ideal platform for beginners and hobbyists who want to experiment with AI and machine learning. Conclusion: The Future of Edge AI As AI continues to evolve, it’s clear that edge computing is a growing area of interest, enabling AI-powered applications to run on small, efficient devices. Whether you’re working with Nvidia’s Jetson series, Google’s Coral Dev Board Micro, or even older STM32 microcontrollers, there are a variety of platforms available to suit different use cases. For companies or developers who need powerful, real-time AI processing, solutions like Nvidia Jetson Nano or Coral Dev Board Micro offer substantial computing power with low power consumption. On the other hand, those working in more cost-sensitive, embedded environments may find great value in deploying AI models on traditional microcontrollers like the STM32 or Raspberry Pi. The exciting
How to Maintain Code Quality While Maximizing Reusability in Embedded Systems?

How to Maintain Code Quality While Maximizing Reusability in Embedded Systems? Ensuring High-Quality Code for Embedded Systems: Best Practices and Tools Despite remarkable advancements in technology, remotely updating embedded systems remains a complex challenge. For embedded software engineers, ensuring robust code quality is paramount, even more so than in other areas of software development. Given the unique nature of embedded systems, careful attention to code quality, scalability, and the ability to handle dynamic product goals and market forces is essential. Here’s an exploration of the tools, strategies, and best practices embedded specialists are using to develop and maintain high-quality code that meets evolving requirements. Key Tools for Maintaining Code Quality in Embedded Systems One of the key challenges in embedded systems development is ensuring that updates are seamlessly deployed across devices. Automating the build, test, and deployment processes is essential, and tools that facilitate continuous delivery (CD) and integration (CI) have proven highly effective. Continuous Delivery (CD) Tools To ensure a smooth and automated deployment process, using industry-standard CD tools is crucial. Popular platforms like GitHub, GitLab, Jenkins, and Azure DevOps help automate the creation of executables (binaries) that are ready to be flashed onto devices. These platforms enable efficient workflows for building, testing, and packaging embedded applications, ensuring code is consistently deployed to different environments. These tools support a robust setup that allows every code change to trigger automated tests, preventing any new code from being merged into the main production code without passing necessary verification gates. This includes static code analysis to catch potential errors or bugs before they can affect the system. Static Analysis and Code Quality Static analysis is an indispensable part of the code quality assurance process. Tools for static code analysis check for errors, potential vulnerabilities, and performance bottlenecks that may not be immediately visible during development. By integrating static analysis into the development pipeline, teams can identify issues early, improving the overall robustness of the system. Tools like Clang Static Analyzer, SonarQube, and Coverity are frequently used in embedded environments to enforce these standards. Containerized Development Environments Consistency in development environments is a major challenge in embedded systems development, especially when multiple developers and teams are involved. Containerized environments have become an effective solution to this problem. Containers ensure that everyone works in the same environment, eliminating issues like “it works on my machine.” A container for embedded systems development typically includes: Compilation Toolchain: Necessary tools to compile code for embedded targets. Static Analysis Tools: To continuously monitor and improve code quality. Debugging Tools: To diagnose and fix issues effectively. Libraries and Dependencies: Pre-installed libraries to support application development. The advantage of containers is clear: new team members can get up and running quickly, and updates to the development environment are instantly propagated to all team members. However, licensing challenges can arise, especially if the project relies on proprietary tools. In such cases, leveraging open-source alternatives can reduce costs and simplify development. Virtual Machines as an Alternative Another approach is using virtual machines (VMs), which offer similar benefits to containers but with some trade-offs. VMs provide isolated environments, ensuring that the development setup is identical across all team members. However, they are more resource-intensive compared to containers, requiring significant computing power to run effectively. Automated Testing in Embedded Systems Development Automated testing is a fundamental part of ensuring code quality and functionality in embedded systems. By running automated tests after every code change, teams can ensure that new changes do not introduce regressions or break existing functionality. The main types of automated tests for embedded systems are: 1. Smoke Testing Smoke tests are the first line of defense in ensuring that a device’s most critical features function as expected. These tests verify basic functionality—such as turning the device on and ensuring it doesn’t catch fire! Smoke tests help confirm that the embedded system is “alive” and can perform its essential tasks before more extensive testing is carried out. 2. Integration Testing Integration tests validate that all components of the codebase work together after changes are implemented. These tests ensure that different modules of the system can interact as expected, providing confidence that the overall system functions properly in a real-world scenario. Integration tests typically run in the same environment as smoke tests, but with a more thorough examination of system interactions. 3. Unit Testing Unit testing breaks down the code into its smallest components, testing each one individually. This is especially useful in Test Driven Development (TDD), where tests are written before the code. Popular frameworks for unit testing in embedded systems include Gtest, Catch2, and Unity (for C projects). Given the hardware-centric nature of embedded development, mocking frameworks like Gmock, FakeIT, and Cmock (for Unity) are essential to simulate hardware interactions and isolate software components during testing. Additional testing techniques, such as fuzz testing and hardware verification tools, may be employed depending on the product’s requirements. Code Reusability and Modular Design One of the best practices for embedded software development is creating code that is reusable and modular. Reusability ensures that the same code can be deployed across different products, saving time and reducing duplication. This is particularly valuable for embedded engineers who design firmware that will be used across multiple devices or platforms. To facilitate this, embedded engineers should think of firmware as a set of logical modules. Each module should be designed to be reusable in different contexts, and any updates or bug fixes to a module should propagate across all products that use it. Tools like CMake, Meson, and Bazel are essential for managing complex build systems and organizing the firmware compilation process, especially when targeting different hardware architectures. Unit testing individual modules is also key to ensuring that these modules can be easily adapted for use in different contexts. By maintaining clean, modular code, teams can speed up development and reduce the risk of introducing bugs when repurposing code for new products. Accelerating Development with External Expertise While implementing these best practices and tools is critical for
Power Management Techniques in Embedded Systems
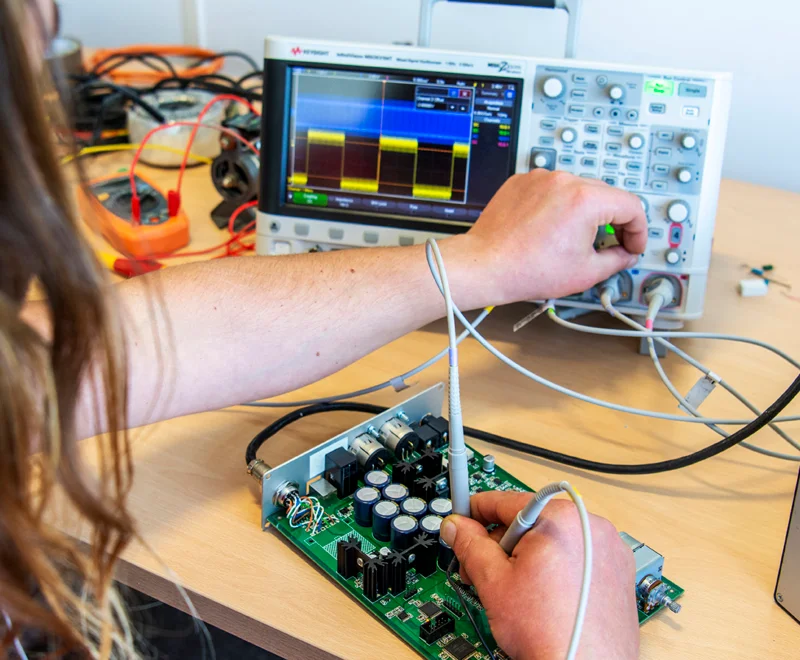
Power Management Techniques in Embedded Systems Power management is critical in embedded systems, directly influencing their efficiency, reliability, and longevity. It involves strategies to minimize power consumption while ensuring that the system operates correctly. Here’s an overview of the techniques used in power management, including their benefits and challenges. Understanding Power Management vs. Power Efficiency While often used interchangeably, power management and power efficiency have distinct meanings: Power Efficiency refers to how effectively a system utilizes the power it consumes, such as extending battery life. This is especially important for embedded systems that are difficult to access once deployed, like those used in deep-sea environments. Power Management is the active process of controlling power usage within a system, including detecting inactivity and shutting down components to conserve energy. Both concepts are interrelated and crucial for reducing overall power consumption. Methods of Power Management Power management techniques fall into two broad categories: hardware and software. Each approach has unique methods to achieve lower power consumption. 1. Software Power Management Techniques These techniques can be applied during both the design and runtime phases. Some key strategies include: Sleep Modes: Initiating sleep or low-power modes when devices are inactive helps conserve energy, similar to standby modes in personal computers. Dynamic Voltage and Frequency Scaling (DVFS): This technique adjusts the CPU’s voltage and frequency according to the workload, reducing power consumption when full processing power is not needed. It allows devices like smartwatches to extend battery life by slowing down operation during low-power conditions. Power Gating and Clock Gating: Temporarily disabling unused peripherals or components reduces power consumption without sacrificing functionality. Optimized Code: Writing efficient code that minimizes CPU operations can significantly lower power usage, making systems like Linux kernels popular in embedded applications due to their customizability. 2. Hardware Power Management Techniques Hardware approaches focus on optimizing power use from the design stage and during runtime. They can be categorized into: Static Power Management: Techniques developed during design to optimize both software and hardware for low power consumption. Dynamic Power Management: Adjustments made during runtime based on system behavior to control power more effectively. Modern components are designed to be low power, with some systems theoretically achieving decades of battery life in standby mode. However, processors often consume significant power, necessitating active management strategies, such as integrating energy-saving features that activate when certain thresholds are reached. Key Considerations for Power Management Integrated Approach Effective power management in embedded systems requires a combination of software and hardware techniques. A poorly designed device can waste power regardless of software optimizations, while ineffective software can drain batteries quickly even with efficient hardware. Pros and Cons of Improved Power Efficiency Advantages: Enhanced Battery Life: Longer operational periods between charges are critical for embedded systems, especially in remote applications. Reduced Maintenance Needs: Efficient systems require less intervention, lowering costs and improving reliability. Lower Operating Temperatures: Optimal power usage can reduce thermal issues, enhancing system reliability. Noise Reduction: Efficient devices often generate less heat and noise, which is beneficial in sensitive environments. Environmental Impact: Improved power efficiency contributes to sustainability by reducing energy consumption. Disadvantages: Development Costs: Implementing power-efficient designs can be expensive and time-consuming, impacting project budgets. Risk of Over-Optimization: Poorly executed optimizations can lead to increased power consumption instead of the intended reductions. Solutions for Power Consumption in Embedded Systems To achieve optimal power consumption, it’s essential to thoroughly integrate power management solutions into the design process. Here are some strategies: Holistic Design Considerations: Evaluate power consumption from the outset of development, considering both hardware and software interactions. Incorporate Advanced Features: Use features like hibernation modes, wake-on-LAN, and better battery management systems to enhance efficiency. Optimize Application Code: Streamline code to minimize CPU operations and peripheral tasks, leveraging more efficient algorithms and libraries. Conclusion As embedded systems become more powerful and complex, mastering power management techniques is vital for developing reliable and efficient devices. By carefully balancing hardware and software strategies, engineers can significantly enhance the longevity and performance of embedded systems, making them suitable for a wide range of applications. Prioritizing power management during the design and development phases ultimately leads to better, more sustainable products.
5 Ways Aerospace Product Development Addresses Real-Time Challenges in Space
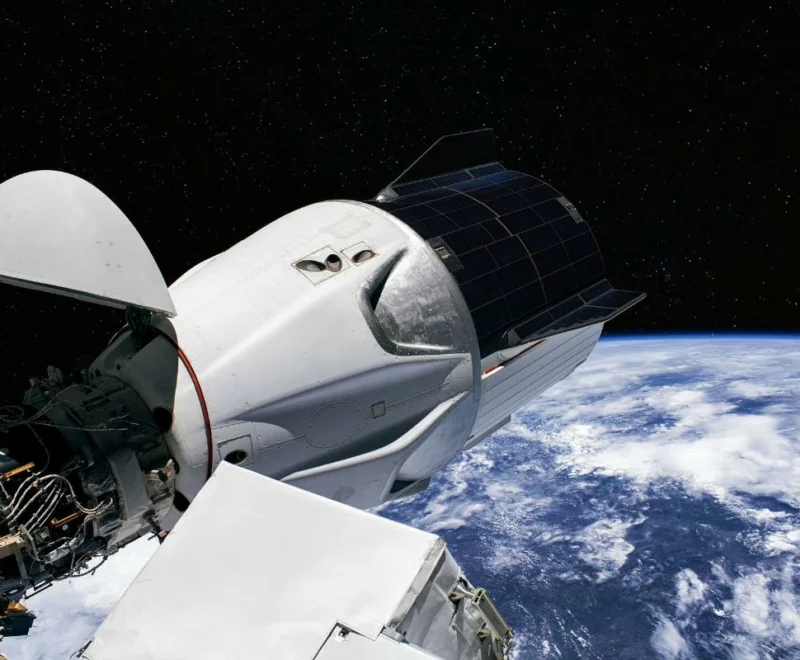
5 Ways Aerospace Product Development Addresses Real-Time Challenges in Space The space industry is at the forefront of innovation, with the global space economy projected to reach $1 trillion by 2030 (McKinsey & Company, 2023). However, the challenges of operating in space are immense, with high stakes and risks that can lead to catastrophic failures. Here’s how aerospace product development tackles these real-time challenges. Challenge 1: Detecting and Isolating Faults The harsh conditions of space—such as radiation, extreme temperatures, and micrometeoroid impacts—pose significant risks to spacecraft and their systems. If left unchecked, these hazards can lead to component failures, jeopardizing missions. To counteract this, aerospace engineers employ Fault Detection, Isolation, and Recovery (FDIR) systems. FDIR continuously monitors sensor readings and system behavior to identify anomalies. Once a fault is detected, it pinpoints the root cause and initiates corrective actions, enhancing system availability and minimizing downtime. Challenge 2: Prognostics and Health Management In space, predictive maintenance is crucial due to the complexity and finite lifespan of components. Traditional methods, such as conditional maintenance, are labor-intensive and not always accurate. Recent advancements in machine learning have enabled Predictive Maintenance (PdM), which analyzes historical data and multiple sensor readings to estimate the remaining useful life of components. The aerospace industry is now exploring Prescriptive Maintenance (RxM), which not only predicts when replacements are needed but also provides proactive guidance for preventing failures. This approach could reduce maintenance costs by up to 30%, although it faces challenges in complexity, validation, and data quality. Challenge 3: Slow Communication Radio communication, while historically effective, struggles with latency and bandwidth over long distances. For instance, while modern satellites can achieve high download speeds, spacecraft like the Mars Rover can only manage 2 Mbps, and Voyager 1 transmits at just 160 bits per second. To overcome these limitations, the aerospace sector is investigating laser communications. This technology can achieve data transfer rates up to 100 times faster than traditional radio signals and maintain signal strength over vast distances. NASA’s Deep Space Optical Communications (DSOC) experiment has already successfully transmitted high-bandwidth data from 16 million kilometers away, marking a significant advancement in space communications. Challenge 4: Power Management Spacecraft operate on limited power sources, making effective power management critical. With the high costs of launching technology into space, every milligram counts, necessitating lean designs for power systems. A well-designed power management system optimizes power distribution and storage, ensuring critical systems have access to power when needed. This involves a combination of software that manages power utilization and efficient hardware design to minimize losses and provide backup options in case of primary source failure. Challenge 5: Bugs As the industry increasingly relies on AI and automation, the risks of software errors become more pronounced. For instance, a coding error in Boeing’s CST-100 Starliner caused a failure to dock with the International Space Station, due to incorrect time settings derived from the launch vehicle. Such incidents underscore the importance of rigorous testing and quality assurance in software development. Implementing stringent software checks is essential to mitigate the risks associated with automated systems and ensure mission success. Conclusion The challenges of aerospace product development are significant, with high stakes and narrow margins for error. Every component, material, and software element must be designed, constructed, and tested to the highest standards. As the space industry becomes more accessible, it is crucial that safety and quality are prioritized, ensuring successful missions for both established organizations and emerging startups in this exciting frontier.
Qt: An Embedded Developer’s Perspective
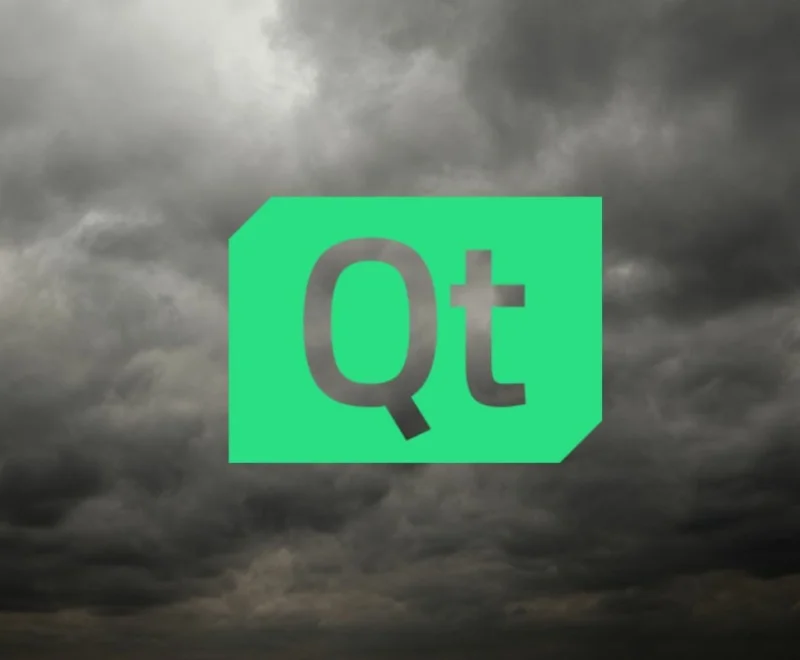
Qt: An Embedded Developer’s Perspective Introduction Welcome to the second part of our blog series exploring the pros and cons of using Qt for embedded systems. In the first part, Bluefruit founder Paul Massey highlighted the business and Agile advantages of Qt. Now, Senior Developer Ben Watts-Jones shares a more cautious perspective, outlining potential pitfalls that teams should consider before adopting Qt. Acknowledging Bias It’s important to recognize that Bluefruit specializes in developing software for embedded systems, often utilizing system-level languages like C++ for precise hardware integration and performance. For us, safety, reliability, and robustness are critical. While we don’t typically require complex animations or advanced graphics, we do seek user interfaces that surpass basic bare-metal frameworks. This is where Qt comes into consideration. That said, opinions on Qt can vary widely depending on the project context. Key Considerations for Using Qt 1. Don’t Use Qt for Everything The allure of a single codebase for multiple platforms can be tempting, especially for business stakeholders. However, this approach has its downsides. For instance, using Qt/C++ to compile for WebAssembly may limit the advantages of standard web technologies, while mobile applications built with Qt might miss out on native functionalities. Moreover, maintaining a unified codebase can complicate documentation and debugging. Each platform may have its own native frameworks, like Apple’s SwiftUI for iOS, which could lead to unnecessary complexity. The costs of managing a non-native codebase can outweigh the benefits, so it’s essential to weigh the trade-offs carefully. 2. Don’t Get Locked In When deciding on Qt, focus on modularity and clean dependencies rather than viewing it as the sole solution. Qt offers numerous modules that can enhance your application, but they can also increase your dependency on the framework, making it harder to pivot later. Aim for a thin GUI layer that interfaces with your core business logic through well-defined APIs. This approach allows for easier transitions between frameworks in the future and enables more effective unit testing without tying your business logic to a specific UI implementation. Ultimately, Qt should adapt to your needs, not dictate your architecture. 3. Consider Your Testing Strategy While Qt provides testing frameworks like Squish, their effectiveness varies. Often, these tools test Qt’s implementation details rather than the actual GUI behavior. If your Qt layer is thin, much of your application logic can be tested independently. For GUI-specific testing, consider end-to-end strategies. Simulate the application environment, perhaps using OCR to verify text changes after user interactions. However, be aware that this method can be brittle due to potential OCR errors or unexpected UI changes. Ultimately, no perfect solution exists for GUI testing, but Qt recognizes the importance of testability compared to some other frameworks. 4. Collaborate Early Qt’s capabilities for responsive and accessible design require thoughtful planning from the start. Retrofitting these features later can be challenging. Unlike web design, which allows for more flexibility with scrolling and scaling, Qt doesn’t adapt as easily. When planning your project, ensure that designers, developers, and stakeholders collaborate early to address issues like text size and localization. This helps prevent scenarios where initial designs seem functional but lack the flexibility to accommodate diverse user needs. 5. Mileage May Vary Qt can be a strong option for certain embedded projects, but it should be viewed as just one of many tools available. Prioritize a well-designed, modular architecture with clean dependencies to maintain flexibility and long-term viability. Emphasize your core business logic and embrace collaboration to enhance responsive design and accessibility. Should You Use Qt for Your Project? Ultimately, whether to use Qt—or any framework—depends on your specific project requirements. The software development landscape is continually evolving, including licensing models and available functionalities. When starting a new project with GUI needs, carefully evaluate all options. Consider factors like project scope, resource limitations, and business objectives to make an informed decision. By understanding Qt’s principles and keeping abreast of developments in the field, you’ll be well-positioned to select the right GUI toolkit for your next endeavor.
Can TDD Enhance Safety in Aerospace Software Development?
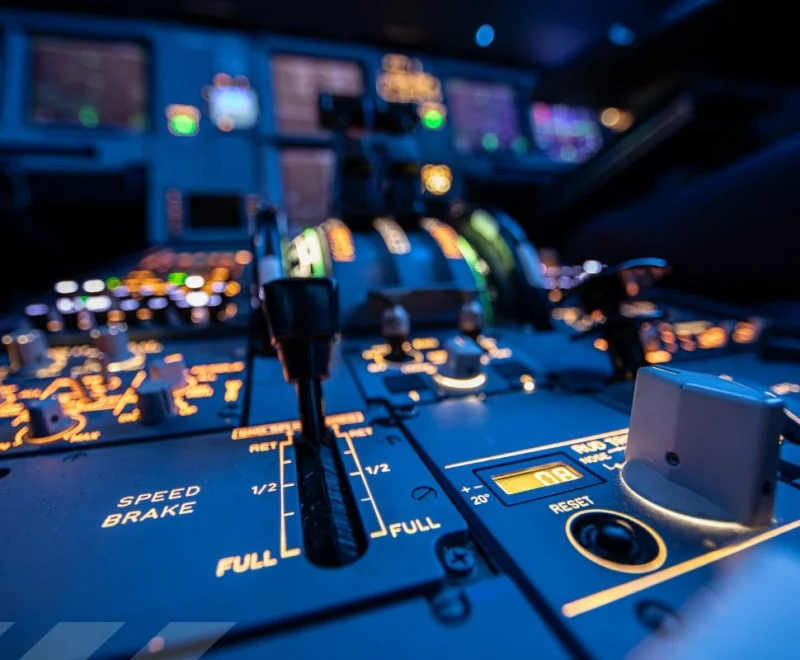
Can TDD Enhance Safety in Aerospace Software Development? The Need for High Standards in Aerospace Software In the aerospace industry, software quality is paramount. The consequences of programming errors can be catastrophic, impacting not just finances but also lives. Despite stringent regulations aimed at minimizing software failure, many current practices focus on late-stage defect detection, which can be inefficient and costly. So, how can aerospace software quality be improved while still complying with DO-178C? Learning from Past Failures Software has a complicated history in avionics, integral to critical systems in aircraft, spacecraft, and ground control. Unfortunately, poor coding practices have led to significant incidents, resulting in billions in losses and the tragic deaths of many. Recent years have seen software errors contribute to the failures of notable projects like the Airbus A400M, SpaceX CRS-7, and two Boeing 737 MAX jets, among others. Understanding DO-178C and TDD DO-178C is the primary standard governing software development in aviation. It provides a structured framework aimed at enhancing safety and reliability, emphasizing thorough documentation, traceability, and testing. However, the standard’s rigorous requirements often push developers toward linear methodologies like Waterfall or V-model, which can make Agile practices difficult to adopt. Test-Driven Development (TDD), on the other hand, can complement DO-178C by enabling iterative testing within the development process. What is TDD? TDD is a development approach where tests are written before the code. The process involves: Writing automated unit tests that initially fail. Developing just enough code to make the tests pass. Refactoring the code to improve clarity and maintainability while ensuring functionality. This method promotes well-tested code from the start, leading to operational efficiency, reduced costs, and higher quality products. How TDD Benefits Aerospace Development While DO-178C outlines what software must accomplish, it allows flexibility in how to achieve it. Here’s how TDD enhances compliance with DO-178C: Early and Continuous Testing Traditional DO-178C processes often create long feedback loops between coding and testing, making early error detection challenging. TDD fosters a tight feedback loop, allowing developers to quickly identify and resolve issues as they arise, saving time and reducing development costs. Thoughtful Design While DO-178C emphasizes thorough testing, it may overlook potential design flaws. TDD begins with writing failing tests that specify expected behaviors, encouraging developers to think critically about design upfront. This results in modular, well-structured code that is easier to test and maintain. Maintainable Code DO-178C ensures code meets functional and safety-critical requirements but does not prioritize code readability and ease of modification. TDD encourages writing simple, focused code that meets defined tests, leading to cleaner, more maintainable software. These tests serve as living documentation, clarifying intended behavior and making future modifications less error-prone. Striving for Excellence Safety-critical industries rely heavily on standards to ensure quality. While these frameworks may lag behind modern coding practices, they establish a baseline for software development. Companies committed to quality should not only meet but aim to exceed these standards. Employing TDD, along with pair programming and clean coding principles, can significantly enhance software quality in the aerospace sector.